인간이 들을 수 있는 주파수 범위를 가청 주파수 범위(Aaudible frequency range)라고 합니다.
그리고 그 이상인 즉, 20KHz이상은 초음파(Ultrasound)라고 합니다.
인간은 듣지 못하지만 박쥐나 돌고래 등의 동물이 이 초음파 영역대를 감지 할 수 있습니다.
초음파(Ultrasound)는 에너지가 작은 단파장(short wave)이어서 장거리 나 장애물을 통과할 수 없고 쉽게 감쇠 됩니다.
하지만 이 초음파(Ultrasound)영역대는 다른 배경 소음(Background noise)과는 확연히 구별되는 특징을 가지고 있습니다.
이러한 초음파의 특성 때문에 산업현장의 예지 보전 또는 예측 보전(Predictive maintenance)에 활용되기도 합니다.
또한 진동 스펙트럼(0-10kHz)보다 훨씬 이른 초음파 스펙트럼(>20kHz)에서 결함을 볼 수 있다는 장점이 있습니다.
공기 중 초음파(공기 중 이동 중인 초음파)와 구조물 결합 초음파(펌프 케이싱과 같은 물질 내 이동 중인 초음파)는 서로 다른 사용 사례에서 사용할 수 있습니다.
초음파 진동 모니터링은 다음과 같은 기계 결함 또는 결함을 효과적으로 예측하는 기법이 될 수 있습니다.
초기 베어링 결함
윤활 문제 - 윤활 과다 및 부족 모두
압력 및 진공 시스템의 누출 감지
증기 트랩, 밸브, 씰 및 개스킷 누출 감지
전기 시스템의 코로나, 아크 및 추적
낮은 RPM(최대 1RPM) 자산 예측 유지보수.
그럼 어떻게 초음파(Ultrasound)를 측정할 수 있나요?
공기를 통해 전달되는 초음파의 경우 아래와 같은 정밀 측정용 마이크로폰(IEPE) 타입 센서를 이용해 측정하며
구조를 통해 직접 전달되는 초음파의 경우 아래와 같은 정밀 측정용 진동 가속도센서(IEPE) 타입 센서를 이용하여 측정 합니다.
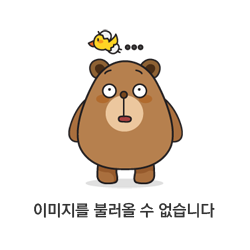
마이크로폰 CRY343 & CRY548
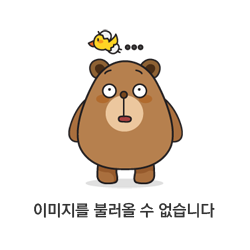
UEB332 초음파 진동센서(CTC사)
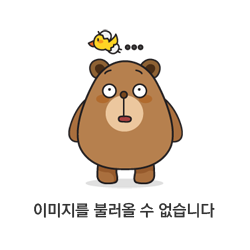
마이크로폰 & 진동 가속도센서를 이용한 초음파 측정
마이크로폰 및 진동 가속도 센서 선택 시 다음 사항을 고려해야 합니다.
- 신호대 잡음비(SNR) *Signal to Noise Ratio
- 감도(Sensitivity)
- 측정 주파수 범위(The frequency range)
- 공진 주파수(Resonant frequency)
초음파(Ultrasound)는 초기 결함의 발생을 매우 일찍 알 수 있기 때문에 예지 보전을 위한 매우 유용한 도구 중에 하나 입니다.
초음파를 측정하여 주파수 분석(Frequency Analysis)를 통한 스펙트럼 분석으로 추가 적인 분석을 할 수도 있습니다.
또한 윤활 문제를 식별하기 위한 매우 좋은 진단 기법이기도 합니다.
윤활 문제를 제때 해결하면 베어링 및 회전 부품의 추가 손상을 방지할 수 있습니다.
베어링 결함과 윤활 결함에 초음파를 사용하는 두 가지 주요 방법이 있습니다.
1. 전체(정적) 측정 트렌드 분석(Trending overall analysis-static)
2. 시간 또는 주파수 영역의 파형(동적) 분석 (Waveform or Frequency analysis- dynamic)
Overall Analysis(총량 값 분석)
Overall Analysis(총량 값 분석)를 위해서는 다음과 같은 두 가지 측정값을 사용 합니다.
1. RMS
2. Peak
초음파 Overall Analysis(총량 값 분석)의 경우 마이크로볼트당 데시벨(dBµV) 또는 데시벨(dB) 측정 단위를 사용할 수 있습니다.
측정 값
|
예상 결함
|
8~10dB
|
윤활 불량 또는 조기 베어링 고장
|
10~15dB
|
2단계 베어링 고장
|
15~30dB
|
후기형 베어링 고장
|
> 30db
|
베어링 고장
|
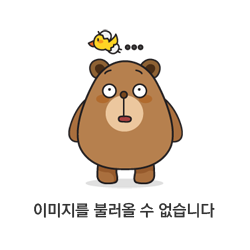
시간 파형 분석(Time waveform analysis)은 시간 영역에서 초음파 신호를 분석
초음파 결함 분석의 경우 FFT 분석보다 이 방법이 선호됩니다.
결함의 초기 단계에서는 시간 영역에 영향을 볼 수 있습니다.
이후 단계의 결함에서는 이러한 영향이 주기적인 간격으로 발생합니다.
충격 지속 시간은 베어링의 결함 빈도와 관련이 있습니다.
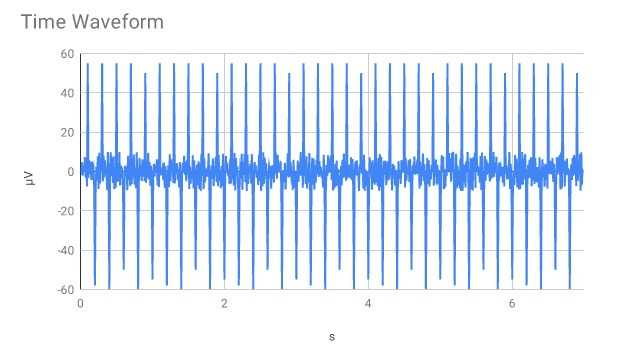
위의 시간 영역 그래프는 0.1초마다 주기적으로 발생하는 충격을 보여줍니다.
이는 베어링의 외측 레이스 결함 주파수에 해당합니다. 충격의 진폭은 결함의 심각도를 잘 나타냅니다
주파수 분석(Frequency Analysis)을 통한 결함 분석
피크가 그다지 뚜렷하지 않은 반복 신호(예: 사인파)의 경우(예: 평균값으로부터의 편차가 작은 경우) FFT를 분석 도구로 사용해야 합니다.
베어링 결함의 초음파 신호는 강한 Impulsive 형태이며 주기성이 없습니다. 이러한 신호는 충격 피크가 뚜렷하고 에너지 레벨이 낮은 과도 신호입니다. 따라서 주파수 영역 내 베어링 결함의 초음파 신호를 분석하기 어렵습니다. 이러한 신호의 FFT는 대부분의 결점을 마스킹합니다.
그러나 FFT는 예를 들어 전기 시스템의 코로나, 아크 및 추적과 같이 초음파 신호에 매우 뚜렷한 피크가 없는 경우에도 사용할 수 있습니다.
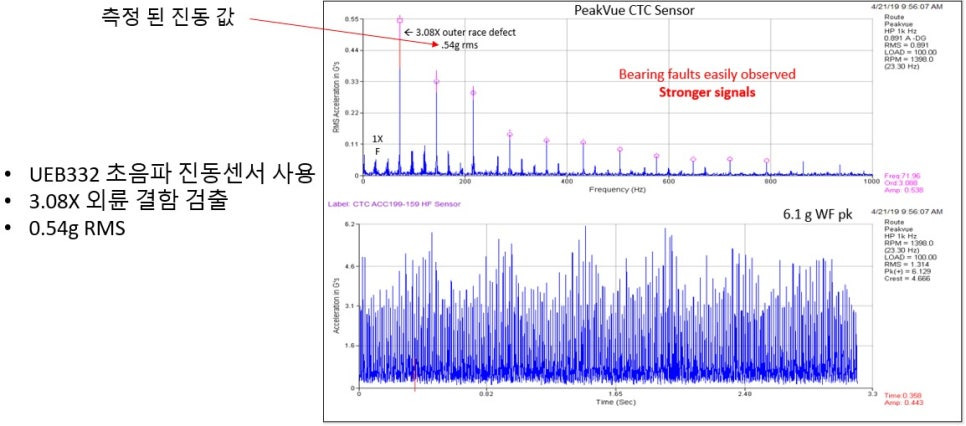
저속(Low RPM)회전 설비에서의 초음파 예지 보전의 장점
낮은 RPM(최대 600RPM 미만) 회전 기계의 모니터링에는 세 가지 주요 문제가 있습니다.
1. 낮은 RPM 기계에서 발생하는 진동 진폭(g 레벨)이 너무 작아서 감도가 높은 가속도 센서가 필요합니다.
500mV/g 또는 1.000mV/g 이상의 높은 감도를 가지는 가속도 센서를 추천 합니다.
2. 결함 주파수의 대부분은 RPM의 0-50x 차수 범위 내에 있습니다.
1Hz와 같이 RPM이 낮으면 0-50Hz의 매우 낮은 주파수 대역이 될 수 있습니다.
노이즈로 인해 이 저주파에서 작은 가속도를 측정하는 것은 어려우며 이러한 노이즈는 낮은 주파수에서 더 두드러집니다.
3. 가속도를 적분하여 속도(Velocity) 값을 보면 노이즈가 더 증가합니다. 따라서 낮은 RPM 기계에서는 속도(Velocity) 측정이 어렵습니다.
저속 RPM 기계에서 진동(가속도 및 속도)을 측정하려면 감도가 매우 좋은 가속도계가 필요하며 매우 높은 분해능(Line of Resolution)에서 데이터를 취득해야 합니다. 분해능이 증가하면 취득해야하는 표본의 수가 증가합니다. 따라서 더 많은 메모리가 필요하고 측정 시간이 늘어납니다.
이는 데이터 취득에 필요한 장비 비용과 인건비가 증가할 수 있습니다.
이에 대한 더 나은 대안은 초음파 측정입니다.
초음파는 RPM의 배수로 측정할 필요가 없습니다. 왜일까요?
초음파는 보통 마찰(두 가지가 마찰) 또는 난류(예: 공기 누출)에 의해 생성되므로 초음파로 쉽게 검출할 수 있습니다.
베어링 결함 및 윤활 문제로 인해 기계의 RPM에 관계없이 초음파 대역에서 마찰 및 충격 소음(음향)이 발생합니다.
고주파 대역이기 때문에 느린 샘플링이 필요하지 않기 때문에 진동 측정에 비해 샘플의 지속 시간이 상당히 짧습니다.
정밀급 마이크로폰 & 진동센서를 이용한 초음파 예지보전은 위의 사례에서 베어링을 예로 들어 설명하였지만
이 외에도 각종 초음파 영역에서 발생하는 가공기나 절삭기, MLCC 절삭기, 스핀들의 마모의 결함 등등 여러 분야에 적용되고 있습니다.
출처: CTC & Sensegrow
https://www.its21.co.kr/product/category.html?c_id=A001
아이티에스(주)
진동센서·소음센서·음향카메라 등을 판매 및 측정 솔루션 제공 전문기업
www.its21.co.kr
'음향센서' 카테고리의 다른 글
다양한 출력(전류,전압,디지털)의 소음 모니터링용 마이크로폰, 소음센서 (0) | 2025.04.14 |
---|---|
소음모니터링용 마이크로폰(소음센서)와 PC 소프트웨어 (0) | 2025.04.14 |
소음센서(마이크로폰) 교정기(캘리브레이터) (0) | 2025.04.14 |
소음 마이크로폰 스페셜(Special) (0) | 2025.04.14 |
½ 인치 마이크로폰을 ¼인치 프리엠프와 연결하여 사용하는 법 (0) | 2025.04.11 |
댓글